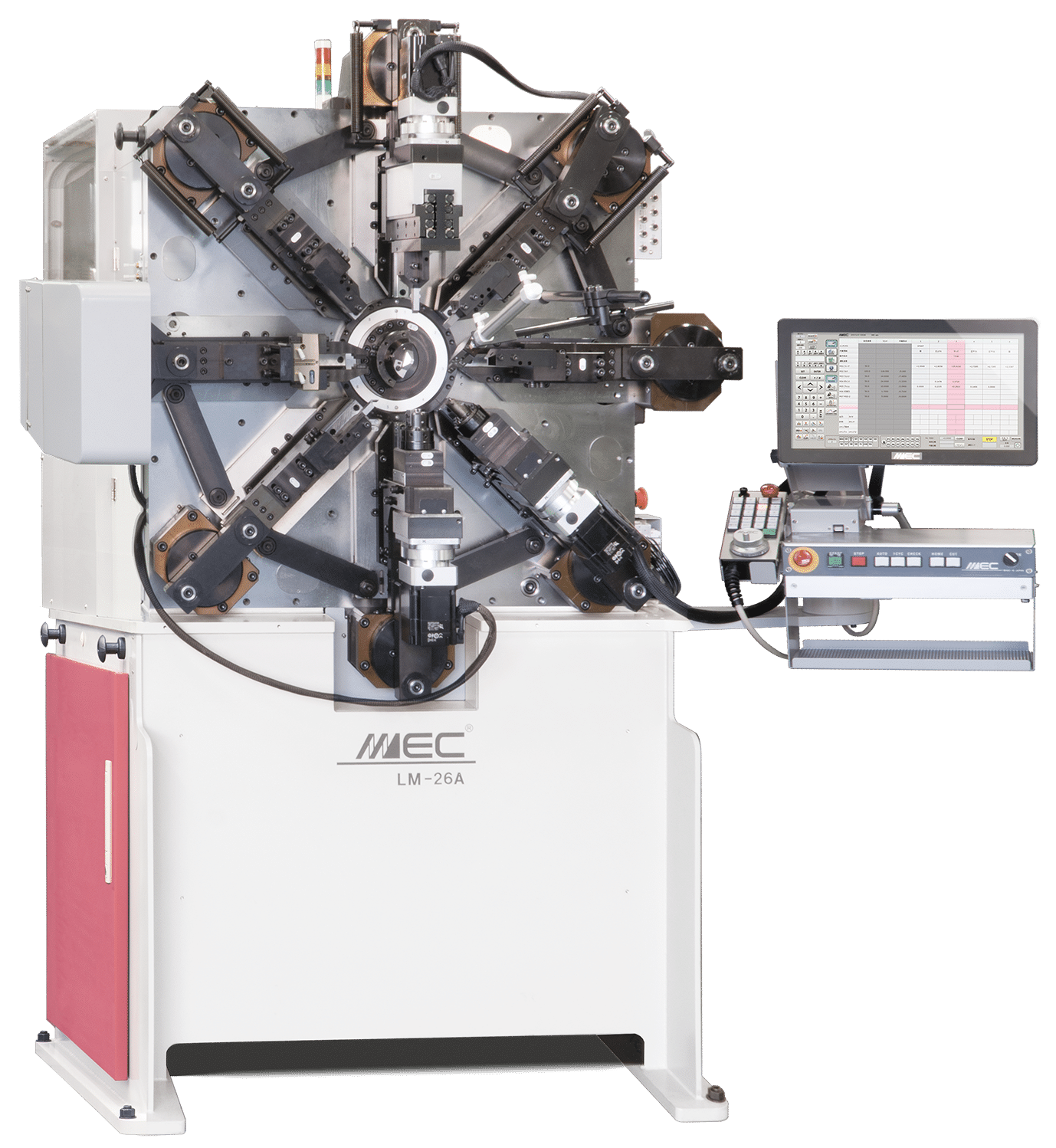
LM-26A Wire Forming Machine
15-axis CNC torsion Spring Machine with Rotating Wire
Intuitive operation has been made possible with a wire rotation mechanism and equipped with eight processing slides as standard.
This machine is equipped with two swinging axes, which control the left and right movement of the facing slides independently.